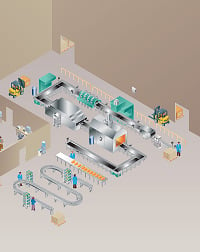
Moving or reconfiguring a production line can disrupt a complex and finely tuned system. When you move a line, electrical distribution systems, variable frequency drives (VFDs), programmable logic controllers (PLCs), lighting, communication circuitry, controls, emergency stop systems, and more are susceptible to unanticipated changes ranging from glitches to outright failures. Glitches and failures at the unit level can in turn cause failures at the system level, such as unexpected tripping of conveyor drive systems, failures of the plant floor communication system, equipment overheating, unsafe electrical systems—and lots of headaches and downtime.
Problems instigated by a move may not be immediately visible when you return a line to service. In fact, symptoms of potentially serious problems may appear long after installation and setup are complete. These potential problems may crop up:
- Motors are noisy or burn out prematurely
- Equipment shuts down for unclear reasons
- Sensors and detectors don't function properly
- Operator complains of ergonomic problems
Outsourcing electrical work is not a panacea
Because electricians and other maintenance personnel are often fully occupied just keeping the facility operating, electrical work for production line moves is often outsourced. While you can usually rely on electrical contractors to follow the requirements of the National Electrical Code for all of the electrical work they do, bear in mind that the code does not require a contractor to address many of the less obvious and frequently overlooked problems, such as voltage drops, harmonics, and EMI (electromagnetic interference).
The contractor's job is to provide an electrical installation "essentially free from hazards but not necessarily efficient, convenient, or adequate for good service or future expansion of electrical use," according to Article 90 of the National Electrical Code. Unless you have made contractual provisions to upsize conductors, use cable specifically designed for VFDs when needed, and the like, you should not rely on your electrical contractor to anticipate and solve many of the subtler issues that may arise, or to plan for future control and equipment concerns or enhancement.
What needs to be done?
Many of the things that need to happen when you move or reconfigure a production line are obvious. You need to:
- design the new layout
- schedule and coordinate each step of the process
- calculate costs
- disconnect, move, and re-rig equipment
- reroute wiring
- reinstall and reconnect equipment
- start up, test, and troubleshoot the reconfigured line
Here are some less obvious requirements for a new or reconfigured setup:
- Find and correct any EMI problems
- Replace worn-out and outdated equipment and upgrade equipment where it makes sense to do so
- Ensure motor drive systems are delivering clean power free of harmonics and at the right voltage after the move
A nine-step electrical system checklist for moving a production line
When engineering is busy getting the production line laid out and operating, the project manager is focused on staying on schedule, and maintenance is tied up keeping the rest of the plant's equipment running, how do you ensure your new electrical installation will work safely and correctly when it's brought back online? How can you make sure upgrade and replacement opportunities are realized? Try using a checklist. It can serve as a map, an agreement about what's to be done (and when and how), and a memory aid to make sure everything gets done.
At a minimum, a checklist should address:
- safety
- power quality
- voltage drop and voltage unbalance
- VFD-related concerns
- grounding
- power and control wiring
- additional items peculiar to your industry, processes, goals, and requirements
You can use the following nine-step checklist as a starting point to help plan your production line move, to keep it on track, to realize the opportunities for replacements and upgrades, and to help troubleshoot when the move is done.
1. Establish benchmarks for existing production line.
Take key voltage and current readings at panelboards and other supply points while the existing line is operating. After the move is complete, you can compare the pre-move readings to readings taken after the move to validate the new setup and to troubleshoot if necessary.
While you are taking the readings, look for any circuits at or near their limits, so you can add capacity to the new line or redesign as needed.
Although taking key voltage and current readings before the move is useful, doing a power quality survey is even better because it gives you a complete picture of the state of the electrical system, including any harmonics, voltage sags, and other problems. Just as when taking voltage and current readings, look for existing problems in the initial power quality survey so you can correct them in the new layout.
Whether you choose to take just key readings or to do a complete power quality survey, be sure to look for voltage imbalances at panelboards, because voltage imbalances can cause three-phase transformers and motors to overheat. You can use a handheld digital multimeter (DMM) or a power quality analyzer to check for variations between the phase voltages in a three-phase system. When using a DMM, any phase voltage reading that deviates by more than 1 percent to 2 percent from the average value warrants corrective action. Power quality analyzers provide a more detailed analysis. The solution for unbalanced voltages is to distribute single-phase loads evenly across all three phases at panelboards and switchboards.
2. Review proposed electrical plans and drawings for new production line.
- Ensure the plans are in compliance with electrical codes
- Verify that the efforts of everyone who is involved in the project are coordinated
After you have made benchmark measurements, review the proposed electrical plans and drawings for the new production line to make sure the plans are the best they can be and accomplish what you want to accomplish.
3. Calculate expected voltage drops.
- Limit the voltage drop at the farthest equipment to 3 percent
The National Electrical Code (NEC) recommends no more than a 3 percent drop in voltage from the last fuse or circuit breaker in the supply to the equipment farthest from the supply. Equipment may not operate properly below its design voltage: computers may lock up, electronic equipment and controls may give spurious alarms or fail completely, and motors may overheat and fail well before reaching their expected 20-year lifespan.
If you think a branch circuit may have more than the recommended 3 percent voltage drop, consider increasing the size of the conductors. Although using larger wire costs more, the cost will be more than offset by the reduction in downtime. Remember, upsizing conductors may require upsizing conduits. Be sure to check the applicable NEC tables.
- Limit the voltage drop for combined feeder and branch circuits to 5 percent
The NEC recommends that a combined feeder and branch circuit should have no more than a 5 percent voltage drop.
Calculate the expected voltage drops for any circuits you are increasing in length or to which you are adding loads.
4. Ensure you have the correct cabling between VFDs and motors.
- Verify that manufacturers' recommendations regarding VFD output cabling and lengths have been met
- Use recommended cabling and add load reactors on VFD outputs as needed
- Minimize electromagnetic interference in communications and control circuits
- Properly ground all systems and equipment
- Run VFD output cables and all control cables in separate conduits
- Keep VFD cables at least one foot away from shielded control circuits and three feet away unshielded control circuits
- If VFD power cables and control cables must cross, cross them at right angles
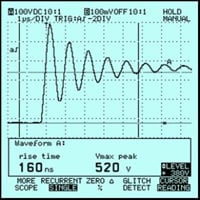
Variable frequency drives (VFDs) are the most common adjustable speed motor drives on plant floors. Because the output of a VFD is a series of sharp-edged voltage pulses (rather than the smooth sine waves of 50- or 60-hertz power), you must give special consideration to the length and type of cable that runs from the drive to the motor, and ensure the cabling is installed correctly. Failure to do so can cause dangerous and destructive reflected waves in the drive cable (Figure 1). Reflected waves can cause higher voltages to appear at motor terminals—as high as 2,000 volts on a 480-volt motor. This increased voltage is a safety hazard, stresses motor insulation, shortens motor life, and can cause immediate motor failure.
If your VFDs were originally set up by a drives specialist (such as a manufacturer's representative), you may have had few or no problems with your VFDs. Changes to that setup, however—and especially changes to cabling—can introduce reflected waves.
5. Evaluate equipment for upgrades and replacement.
- New technologies may be available to improve productivity and reduce energy costs. As a rule, when capital equipment needs to be replaced, get a higher efficiency model.
- Improvements that increase worker safety, comfort, and the general work environment often result in higher productivity and worker satisfaction.
- One of the biggest problems on automated production lines is small power glitches that damage PLCs, so consider adding PLC protection.
- Adding VFDs to control centrifugal pumps and fans can save a lot of money. For example, at 9 cents per kilowatt hour, reducing the speed of a 25-horsepower motor from 1,800 rpm to 900 rpm reduces its hourly operating cost from $1.68 to $0.21, a cost reduction of over 80 percent.
- Moving a production line can also be a good time to upgrade the lighting system. Replacing older T-12 fluorescent fixtures and HID lighting with newer T-8 and T-5 fluorescents reduces lighting costs significantly. Consider change to LED lighting where appropriate.
After the move
6. After the move is complete, check all safety circuits and emergency stops.
- Verify that safety circuits and emergency stops are installed as specified in the electrical drawings
- Verify correct operation of every circuit as part of the production line startup
Installing or reinstalling all required safety circuits and emergency stops and verifying they are working correctly are among the most important tasks to complete when moving or reconfiguring a line. Be sure to understand and comply with the requirements of regulatory agencies (OSHA and NFPA, for example, in the United States), such as sounding warnings before conveyors start, having emergency stops at operator locations, and having emergency circuit resets. PLCs must de-energize outputs when an emergency stop is actuated, and motors must shut down if a PLC goes offline.
7. Verify grounding for safety, code compliance, and electrical noise reduction.
- Bad communications, such as when noise affects the function of a 4-20 mA control loop signal
- Sporadic shutdowns
- Intermittent communications
- PLCs that reset in a seemingly random fashion
- Earth ground devices tripping
- 5 volt supply level going up and down with sensitive equipment
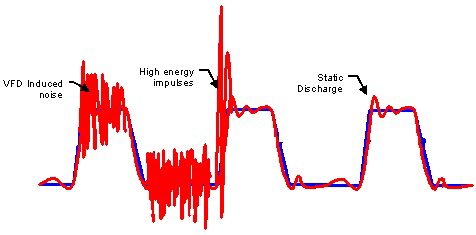
Grounding is a critical consideration when relocating electrical equipment (so much so that it is one of the first things to check when troubleshooting after a line move). Proper grounding is necessary not only for safety and to meet electrical code requirements; it can also reduce the effects of electrical noise. Electrical "noise" is any unwanted electrical energy in an electrical or electronic circuit. The easiest way to detect electrical noise is with an oscilloscope (Figure 2). Noise can cause equipment to operate in an unexpected or less-than-optimal manner. For example, a VFD connected to a motor with unshielded cable can cause 80 volts or more of electrical noise to appear in nearby, unshielded communication wiring, and 10 volts or more of noise to appear in nearby shielded cables. Electrical noise can mean operational problems on the plant floor, which may appear in the following ways during commissioning of the new production line:
8. Complete a power quality survey after installation to identify potential problems and establish benchmark recordings for the electrical maintenance program.
The power quality survey gives you a complete picture of the state of the electrical system, including any harmonics, voltage sags, and other problems. Although taking key voltage and current readings is useful, doing a power quality survey is even better. Benchmark readings are valuable resources for establishing or maintaining an effective predictive maintenance program, if desired.
9. Test the line for correct operation.
Before resuming production, thoroughly test the line for correct operation. This is a good time to bring in line operators and get their feedback. Be sure everyone who was involved with the line move is present when you restart the line so they can assist with troubleshooting and final adjustments.